The earlier blogs in this series highlighted a number of pressing dynamics in the current direction of the RF power packaging ecosystem, starting with global drive for lead-free manufacturing. Next, support for eco-energy consumption (efficiency and sustainability), focus on the engineering and process challenges required by successfully meeting cost and competitive pressures in manufacturing, and finally, the exponential evolution in the wider technologies driving demand.
As a contribution to meeting these challenges, Palomar’s Innovation Center in Singapore has been developing pressure-less silvering sintering capabilities on our 3880 Die Bonder using a Musashi AeroJET dispenser. Silver sintering is commended by its strong cost advantages, high performance, and widespread applications. As essentially a “plug and play” addition to an already outstanding machine, the two extend terrific performance capabilities across a range of additional packaging needs.
As pioneers, Palomar has a natural interest in making processes better and more efficient. In this case, our interests converged with a significant upswing in research on Ag sinter applications on the one hand, and extraordinary (almost instant) practicality on the other. It is not always the “quantum leap” in ideas that can make a profound difference, but something rather more modest—in this case, advanced software design facilitating effective technical synergy between bonder and AeroJET dispenser. Other jet dispensers that have similar features to Musashi were considered and our software can be adapted to work with these.
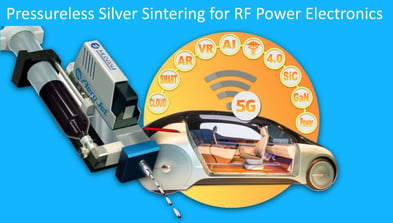
We remind our readers that key parameters such as ease of use, cost effectiveness, accuracy and repeatability, volume potential, environmental constraints, energy consumption, and scalable dynamic with technology evolution were all met. One we have not mentioned is strongly anticipated now and in future commercial demand.
While our Singapore Innovation Center is currently occupied with other projects, we do anticipate further study in other areas such as Transient Liquid Phase Bonding (TLPB,) which uses a thin layer of low melting point material (such as tin) between two thicker layers of material. The rationale is that when the thin layer diffuses into the top and bottom layers, the result is a single phase that has a melting temperature higher than the original thin layer.
As for other future projects, we are currently mindful of the following options:
- Further develop and then stretch the research project we undertook in the first half of A larger and different aspect ratio GaN die would more fully establish process capability. Certainly more “ground” it in commercial and technical pragmatics.
- Our Singapore study was limited in scale and size; other sizes (such as square die) may prove more difficult.
- We are especially excited about innovations in nano-particles and other developments for Ag sinter paste. Material science is another growing area of research leading to improvements—possibly huge practical impacts on packaging technologies and processes— driven of course by performance.
- Conversely, material adaptations may present significant bonding challenges that hold such commercial benefits that they are well worth negotiating.
- Automated optical inspection as an additional “drop in” solution (integration) to these style die bonders may help further improve the speed and consistency of this process; in-situ BLT verification would add another level of process reliability.
- Finally, in an era of exponentially technical, commercial, and competitive change one thing is for sure: this is not an industry where we can rest on past Continual innovation is more imperative than ever.
Speaking of innovation, Palomar now has three innovation type centers globally: at our world headquarters in Carlsbad, California, a newly refurbished center in Singapore, and our new Demonstration/Prototyping Lab at the EPIC Center in the UK. We are always interested in hearing from companies and engineers with challenges and development concepts that can merge our expertise and equipment advantages and yield practical advances.
To learn more about pressure-less silver sintering for RF Power Electronics, download our technical article: Energy and Eco-Sustainability using Pressure-less Silver Sintering for RF Power Electronics.
Read the first 3 parts of this blog: Pressure-less Silver Sintering for RF Power Electronics, Part 1 of 4, Pressure-less Silver Sintering for RF Power Electronics, Part 2 of 4, Pressure-less Silver Sintering for RF Power Electronics, Part 3 of 4