Prepare for Manufacturing
Prepare for Manufacturing is a comprehensive pre-production service designed to help customers minimize downtime, optimize efficiency, and streamline their transition to full-scale production when implementing new Palomar Technologies equipment. Instead of waiting weeks or months to develop a working production process, our expert team works ahead of time to prepare and optimize your manufacturing setup before your equipment is even installed at your facility.
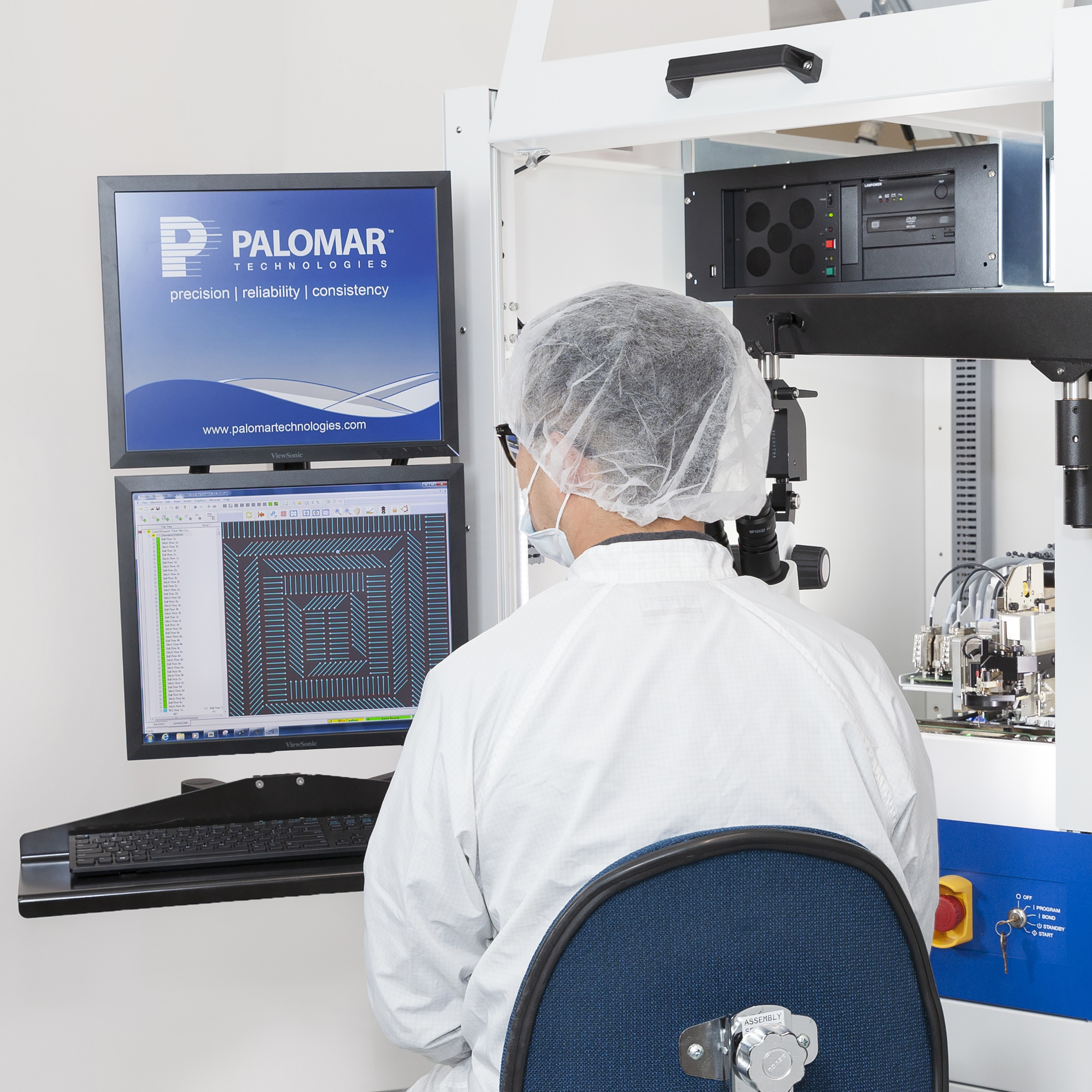
The Challenges of Integrating New Equipment
Many manufacturers invest in cutting-edge equipment but struggle with:
- Long learning curves for operators and engineers.
- Extended product verification cycles to ensure quality consistency.
- Delays in process qualification and commercialization.
- Excessive material waste and labor cost during early-stage trials.
How Does Prepare for Manufacturing Work?
With Palomar Technologies’ Prepare for Manufacturing service, customers receive fully developed, tested, and verified assembly programs tailored to their specific product and process requirements. Our team of experienced process engineers works in partnership with customers to ensure a seamless transition to full production by providing:
- Proven Assembly Programs & Ready-to-Use Processes
- Palomar Technologies develops and optimizes the assembly process based on customer requirements and production goals.
- Customers receive fully functional assembly programs ready to be transferred onto their new equipment.
- The process is tested and validated at scale to ensure high-yield and repeatable results.
- Completed, Quality-Tested Assemblies
- Before equipment installation, Palomar produces fully assembled and quality-checked prototypes or pilot runs.
- Customers gain early validation of their process, ensuring seamless scaling.
- Comprehensive Documentation & Process Guidance
- Customers receive detailed process documentation, including:
- Key process parameters and optimization strategies.
- Potential failure modes and troubleshooting techniques.
- Material recommendations and process-specific best practices.
- This documentation helps accelerate internal approvals and reduce trial-and-error time.
- Training & Knowledge Transfer
- Process engineers gain hands-on experience working with their own products and processes before equipment delivery.
- Palomar’s engineers provide direct training and best practices guidance, helping customers avoid costly mistakes.
- Teams become confident and capable in operating and programming their new equipment from day one.
- Advanced Support & Post-Installation Assistance
- Customers receive a set number of advanced support hours, ensuring rapid solutions to any issues that arise post-installation.
- Palomar’s engineering team remains available for process adjustments, troubleshooting, and optimization guidance.
The Bottom Line: Faster ROI, Lower Costs, and Smoother Transitions
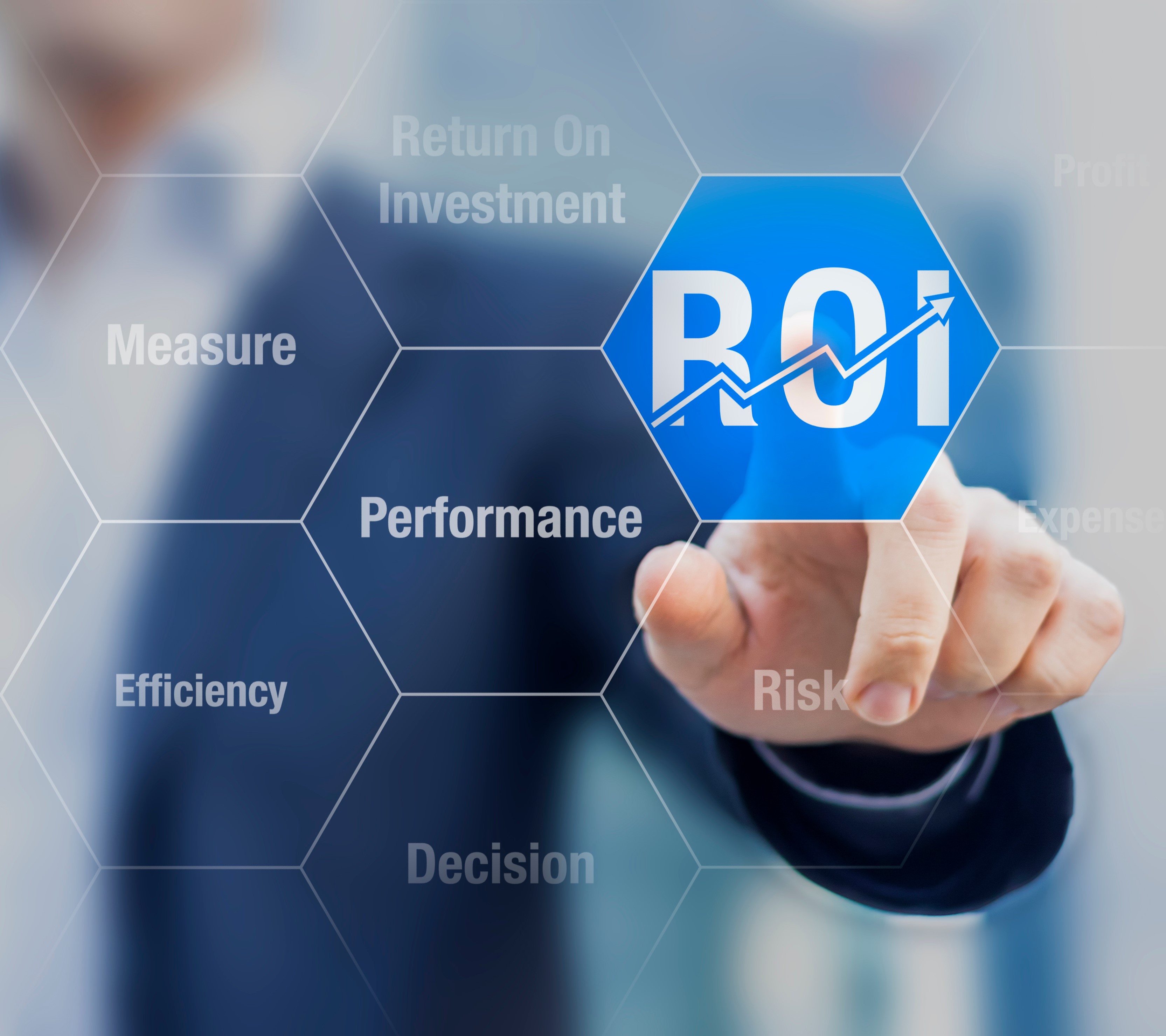
With Prepare for Manufacturing, customers can expect to:
- Save thousands of dollars in labor and material costs by avoiding inefficient trial phases.
- Reduce production ramp-up time by weeks or even months.
- Eliminate uncertainty with a fully validated process, ready before equipment arrival.
- Enhance operator confidence through expert training and process handover.
- Start profitable production immediately, rather than investing resources in troubleshooting.