DIE BONDING
Epoxy die bonding, sometimes referred to as epoxy attach, or even thermal cure epoxy attach is one of the most common die bonding methods in the industry due to its price point and speed. Epoxy die bonding/attach is available in two main varieties, conductive and non-conductive. Conductive epoxy attach can be used in a large variety of applications but generally consists of applying a bed of epoxy underneath a die to form a thermal and electrical connection between the die and the substrate.
Non-Conductive epoxy can be applied to an assembly to provide structural support for components, encapsulation of wire bonds, or even to function as a non-conductive barrier to prevent shorting. Epoxy in general can be deposited onto a surface through dispensing via time-pressure, auger, or jetting, and through daubing or pin transfer.
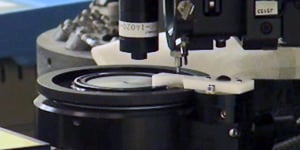
Epoxy applications are quicker than some of the alternatives, such as solder or eutectic, because components can be placed into the epoxy which allows them to retain their positions throughout handling. This is especially beneficial for assemblies which go through a batch cure in an oven later on in the assembly process. Epoxies generally cure at a much lower temperature than what is needed for melting solder. In addition, high force, an inert environment, or scrubbing are not necessary to create a good bond.
Another key benefit to using epoxies is the easy rework potential; even after a component has been attached with epoxy, as long as the assembly has not gone through a cure cycle, the part can be easily reworked.
Epoxy attach is useful for both general die attach and flip-chip processes where fine control of epoxy is required. Palomar’s die bonders can apply tightly controlled, small volumes of epoxy onto bumps for flip-chip attach, while also using automatic pattern recognition to align the bumps and complete the flip-chip application.
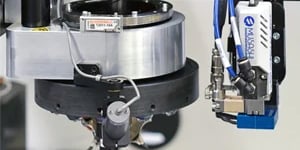