For applications that have strict temperature parameters, eutectic die attachment is typically the best solution. Epoxies and other fluid bonding solutions cannot address high thermal conduction like eutectic die bonds can, making automated eutectic die attach the most viable high-process capability packaging solution. Eutectic die attach is a highly controlled die attach process and is perfect for high-reliability and high-accuracy requirement devices.
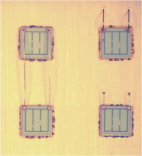
In a wide range of industries from aerospace to defense to medical, automating the optoelectronic device packaging process is a must and eutectic die attach provides an accurate and precise form of component attach.
High-process Capability Packaging Solution Conditions
In order for successful results to be achieved, there are several steps that this high-process capability packaging solution undergoes. During eutectic die attach, the substrate is heating to a temperature just below the solder's eutectic temperature and the thermal conductivity of the metal must be in the correct range while the contact angle on the metal's surface must be minimized. The thermal conductivity of the substrate requires that there is some means of heating the joint area where the solder is placed. However, the applied heat cannot be so excessive that it damages surrounding components. During the bond cycle, an incremental thermal energy is supplied to the solder layer to promote the solder melting process. Liquefied solder then penetrates both bonding surfaces and an intermetallic bond (also known as wetting) develops.
When wetting occurs, the joining surfaces must permit molten solder to wet and spread during the available time window. Issues arise when contaminants are introduced to the surface, referred to as passivation. Passivation layers affect wetting by forming a barrier between the solder and base metal, and these layers are typically oxide films that may be only a few angstroms thick. Other elements, such as nickel, can form passivation films that require fluxes (solvents) or plasma cleaning to remove. Oils, silicones and organics are frequent contaminants that can also form barriers to wetting and act as a passivation layer. Beyond the basic requirements for eutectic soldering, many additional factors contribute to conditions required for a robust solder joint, including die metallization, temperature and the substrate material itself.
Eutectic Die Attach Methods
High-reliability eutectic bonds can be achieved through two heated system configurations: Steady Heater Stage (SHS) or Pulsed Heat Stage (PHS). The decision between the two techniques depends on the preferred process of die bonding as well as material requirements.
- Traditionally used steady state heaters and scrub in the X/Y plane to minimize voiding
- Chosen when AuSn solder is pre-placed on the die, the substrate, or sandwiched between the two. This way, the solder is only heated up specifically when the die and the substrate are in contact and bonding. In this process, Steady Heat Stage would have caused the AuSn to melt and change composition before the die is placed.
- Pulse heat processes and scrub in X/Y and Z axes—much higher placement accuracy attachment as the automated system does not let go of the device being attached until the temperature at the eutectic interface is into the plastic or solid region of the material’s phase diagram.
Advantages of Eutectic Die Attach
Automated eutectic attachment is a leading technique for high-performance and high-capacity die attach applications. The needs of the current industry environment— with high-volume and high-placement accuracy (±5 microns)—clearly call for flexible automated equipment. The most significant advantages of eutectic die attach are its great thermal solder conductivity and its immediate fixing of bonds after die placement.
Eutectic die attachment is also beneficial in preventing:
- Catastrophic Optical Damage (COD): damage to the mirror coating reflects energy back in to the laser and overheats over time
- Reduced Device Longevity: poor thermal interface will require higher current input for desired light output
- "Noise" Feedback: adhesive bonds provide noisy feedback at data rates > 40 Gps
Eutectic bonding’s unique thermal conductivity makes it desirable over epoxy-silver bonding in power device or radio frequency amplifier applications. Attachment fluids such as epoxies cannot address higher thermal conduction, so automated eutectic die attach remains the only feasible high-process capability packaging solution.
To learn more about eutectic die attach, refer to the following resources:
----
Claudia Haskin
Marketing Communications Manager
Palomar Technologies, Inc.