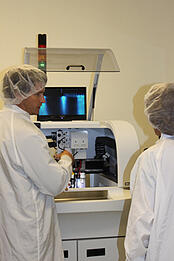
The search for a "complete, yet customized, solution to a microelectronics assembly requirement" is an all-too-common request from a Palomar customer; yet a company's process build can change as their needs, abilities and support system broadens. In the beginning, an organization may only need process development or prototyping support or they may only have small-to-medium quantity builds—a scenario where collaborating with our engineering experts to build, test and perfect product without investing in capital equipment is ideal. In other cases, an organization may want to build product themselves but is limited in the amount of capital funding—a situation where a certified refurbished bonder system becomes an excellent fit. What some wire bonder and die bonder owners may not be fully aware of is the opportunity to expand their proven build process with the unique capabilities and flexibility offered through Palomar's alliance solutions: epoxy dispense (GPD-Global), bond testing and die sorting (Royce Instruments) and manual bonders (Hybond).
Highlighting GPD-Global's capabilities, this company has a long-standing foundation of innovation, hard work and success, earning the title of world leader in dispense technology. While their platforms—such as the Max and Max II series—have the precision and accuracy required in the microelectronics world, it is GPD's dispense pumps that really are the “heart” of the system and allows the rest of the platform to deliver the solution the customer requires. For example, at Palomar, we are often tasked the challenge to pick-and-place very small die. Recently, I was working with a customer on placing a 200µm square LED. One of the challenges of placing a die that small is how to make an epoxy dot that is smaller than the die. One of the methods that Palomar uses on our fully automated die bonder is the “stamp transfer” method where you actually come down into a very thin amount of epoxy and “transfer” the epoxy with a flat bond tool onto the substrate. This can provide 150µm dots; a very effective solution, especially for low-volume or prototyping.
However, what happens if you need medium-to-high volume? Using a capital-intensive, high-accuracy die bonder for stamping dots when you need it to be placing a high-volume of die may not be the most wise approach. This is where the GPD Micro-Dot Dispenser on a Max series platform will do the job, and do it well. While actual dot size is going to be dependent on what material you are dispensing, the Micro-Dot pump works very well for dots smaller than 0.010" (0.25 mm).
The pump works with the following method: Fluid is fed into the auger cartridge from a syringe reservoir pressurized with air. When the auger rotates, fluid moves through the cartridge and is funneled through the dispense tip to the substrate.
The rotation of the auger is precisely controlled by a brushless DC motor with an encoder that can be programmed with specific dispense parameters. The encoder provides more than 57,000 counts per 360-degrees of auger rotation, thereby providing the precision control required for micro-volume dispensing. For the smallest of dispenses, a high-resolution option is offered for attaining 200,000 counts for a single revolution. The Micro-Dot pump can span a wide range of dispense processes with its ability to use a range of auger dimensions.
The dispense process defines the type of nozzle to be used. Standard nozzles for the Micro-Dot have been designed for enhanced flow rate in order to funnel fluid with reduced pressure to eliminate clogging of the nozzle tip. Precision nozzles are available in a variety of lengths and in either ceramic or machined stainless steel.
Standard clearance between the auger and cartridge wall is 0.0003" (7µm). Tolerances are set very high to avoid spheres of solder or other particles from shearing between the auger and cartridge wall. When particles shear, they become deformed and can either lead to clogging of the nozzle or can accumulate on the wall of the cartridge leading to binding. GPD customizes an auger to allow for fillers to float without being damaged. This is where the small dot capability and the repeatability is obtained.
Auger without customization |
|
|
|
At Palomar Technologies, we are focused on providing our customers with the best overall solution. With our alliances, such as GPD, we can better tackle and confidently succeed over the tough challenges of the microelectronics assembly world. Learn more about GPD's line of fluid dispense solutions at www.GPD-Global.com, or feel free to contact Palomar Technologies.
----
Dale Perry
Regional Account Manager, Eastern Americas
Palomar Technologies, Inc.