One frequently asked question when addressing high-power wire bonding applications is “how many wires do I need?” As a common “rule-of-thumb”, each 1 mil diameter (0.001 inch) gold ball-bonded wire is capable of approximately 1 Amp of electrical current per wire. Therefore, the 40 wire system pictured below is capable of ~40 Amps. However, if the device had been wedge-bonded rather than ball-bonded, the wedge-bonded wires’ current carrying capacity would be estimated at approximately 0.6 Amps per wire, so ~40% more wires would be required for the same 40 Amp application.
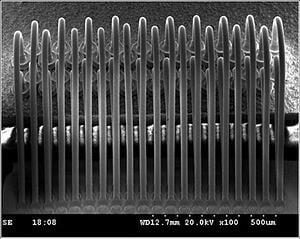
An example of a high-power connection consisting of two rows of staggered wires
Although these general guidelines are widely accepted, there are many other variables that affect current-carrying capacity of bonding wires, which influence failure current—also known as “fusing current”. By accurately specifying wire-bonded connections for high-power semiconductor devices, fusing current can be calculated and theoretical designs can be implemented.
Proper design can enable a device to survive power spikes or, conversely, to fail strategically at a given power level as a failsafe to protect other components within the circuit.
Variables that affect fusing current
- Wire diameter
- Wire length
- Duty-cycle of applied power
- Type of bond used (ball or wedge)
The differences between ball-bonded wires and wedge-bonded wires have a significant impact on the efficiency of heat transfer from the wire to the bonded connections on the chip and package. Significant differences between ball-bonded wires and wedge-bonded wires are the bonded area and deformation of the bonds.
Ball bonds have greater surface area than wedge bonds. However, the second bond in a ball-bonded wire is similar to a wedge bond in that it is pinched—the pinched bond has a smaller contact area than the larger ball and, thus, thermal transfer is reduced in the second bond. To remedy this shortcoming, strategically placed gold ball bumps can be placed either on top of or below the stitch to increase the bonded area, increasing both the surface area and the current carrying capacity of the connection.
Since electrons flow across the surface of the wires, having multiple wires increases the surface area compared to a ribbon. In order for the wire to fail it must heat to its melting point. Since the wires are individually lower in mass than the larger ribbon, heat will dissipate more effectively and evenly, increasing the current capacity because they will run at lower temperature than a solid conductor.
Palomar Technologies will be exhibiting at the Strategies in Light 2011 conference February 22-24 in Santa Clara, CA. Download a free pass to the exhibitors’ show floor and visit Palomar Technologies at booth #238 to discuss gold ball bonding for LEDs.
----Steven BuerkiWorldwide Account ManagerAssembly Services, Palomar Technologies