This is Part 3 of our series on Manufacturing in North America. The following case study is an excellent example of North America's low cost manufacturing status played out in an actual business setting.
Case Study #1 - Who is the Lowest Cost?
In 2007, a U.S. hybrid microelectronic packaging firm lost its Asian high volume assembly partner. The timing was terrible for the U.S. manufacturing firm: they were in the middle of work with a customer building a complex LED module and was ready to transition out of the prototype phase and into the high volume production phase. The U.S. firm was running against time to find a new partner and a new source to do the high volume production for these highly unique and complex LED modules. The firm's U.S. management took a pause to look at what assets existed - what was in house to make this work? How could they solve this problem without fumbling around and wasting time? For one, the U.S. firm was a 35 year steady supplier of premier ultra high accuracy automated microelectronic assembly systems. With this, they had relationships in place to quickly identify prospective high volume suppliers. In order to find the right supplier from the list generated, they defined a generic microelectronic assembly: 35mm x 30mm assembly with 30 LEDs that required <13 micron accuracy, several discrete and passive components, 73 32 micron Au (Gold) wires and encapsulation.
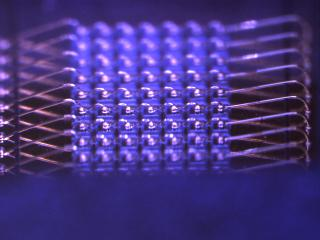
Prospective suppliers where looked at in Asia and North America. Following the first down select based on a questionnaire, the U.S. manufacturing firm asked the remaining suppliers to quote the assembly cost (of the above stated generic microelectronic assembly) for quantities of 5000, 10000, and 20000 per month. The U.S. firm saw a paradigm shift in the world of on-shore vs. off-shore high-tech complex manufacturing with the surprising results:
1) Mexico (Tijuana) was the lowest cost
2) China (Guangdong) was a close second to lowest cost
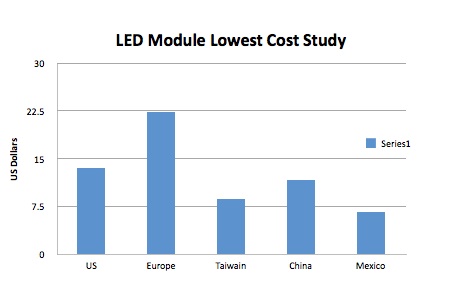
To put these results in context, the data showed that if there is a high degree of automation in the process, labor costs became less important (more automation, fewer operators, less need for labor). It's important to note that automation is the cornerstone in most complex automation because it is the ONLY way to ensure a repeatable, consistent, measurable process. When a part becomes more complicated, the time factor to produce it expands, therefore labor costs increase. Not so with automation. With automation, processes can be done simultaneously and rapidly with little operator intervention and less operator task time.
Defining Complex
The word "complex" describes both the type of package or assembled product as well as the procedures and processes involved in designing and manufacturing the product. With automation making labor it a much less significant factor, the full cost of bringing a complex product from design to market-ready, take center stage. There are many steps between design and market-ready; each step must be accomplished on schedule without sacrificing quality. Delays during any part of the process can prove very costly. Each complex module carries an expensive price tag. Better said, the stakes are higher when dealing with complex modules. So, with the failure of a complex module the cost is greatly magnified. Moral of the story: if you are contracting work out on complex modules, find the manufacturing/assembly firm that has the highest success rate of working parts over the long run.
Why Mexico is Important
The U.S. firm discussed in the above case study is located in San Diego county. Tijuana is approximately a 45 minute drive from their U.S. headquarters. This is a significant aspect in regards to cost, efficiency, time to market, and product quality: the U.S. firm's engineers and management are geographically close the the high volume production site and have hassle free access to crossing the border. The cost of flying around the world to do common tasks are completely eliminated. These tasks include fixing a minor problem, getting a machine back up and running and/or making a small change in the application process.
If you are considering a change of local in your contract manufacturing, consider sense to manufacture in North America today.