This is Part 3 of the Eutectic Die Bonding 101 series. In the previous 2 blogs, we discussed what "eutectic" means, the variables and parameters surrounding the process and the importance of automated temperature control with a Pulse Heat Stage. Anyone performing eutectic die attach wants a "void free eutectic die attach". We discussed the real meaning of "void free" and the financial paybacks that come through using Pulse Heat Profiling (via the Pulse Heat Stage).
Force/Scrub Attach
Scrub, in the eutectic context, can be defined as "application of force in X and/or Y direction". This is typical done over steady state heat.The Scrub motion performs three actions: 1) breaks the oxide layer, 2) drives out voids, and 3) forces solder into die. The platform options that exist are a Hotrail conveyor (low mix, high volume) and a Pulse Heat system.
Let us discuss for a moment a common application: Gold Tin Solder. Scrub works well for Gold Tin Solder especially well because scrub and heat create a "gold rich" mixture, dramatically raising the liquidous temperature of the solder (as seen in the graph below).
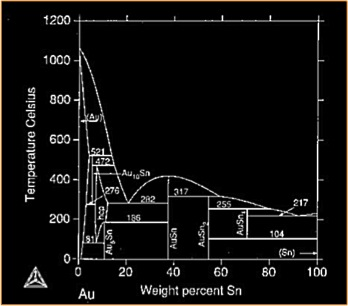
Benefits of Scrub Attach
First off, it is a simple, reliable system. There are two glaring benefits of scrub attach: 1) low cost entry for eutectic attach, and 2) easily reconfigured design.
Secondly, it gives the user "void free" bonding which results in high yield. Any time one combines low cost with high yield in application, the benefit most certainly will be seem in the company's bottom line.
Scrub Attach's Payback
Just as we did with looking at the payback of the Pulse Heat Stage/Profiling in the previous blog, we will look at how Scrub pays you back!
Lets start with some assumptions about Scrub attach:
- 10 seconds saved per attachment vs. Pulse Heat
- 4 attachments/module
- 2 shifts/day
- $50/module (low end RFSOE part), 50% margin
With these assumptions, the user gets 4x throughput (20 sec vs. 60 sec) which is equal to $9,000 per day! Now that is quite significant.
It is important though to look at a few of the drawbacks with Scrub Attach:
1) Materials are brittle; they may be cracked or broken by scrub motion
2) Edge collets are required to grip the die and this may not be an option with restricted geometries and "no-touch" areas. Also, mechanical tolerances may affect accuracy.
3) Post-placement "swim" sometimes occurs - this may be an issue for post-placement accuracies better than 10 microns.
Hard Solder Comparisons
Making the hard solder comparison is important. 80Au20Sn melting temperature of 278C is more thermally stable than SnAgCu at 220C and SnPb at 183C. Now, why are these temperatures important?
Temperature is important for several reasons:
- When the bonding represents the sealing frame for a vacuum cavity, where a "getter" is needed to obtain the required vacuum. Such getters may require activation at high temperature (for instance, 350 oC).
- When chips are to be stacked and bonded in the successive proccesses, as in 3D integration.
- If interconnections and sealing rings are being bonded in different proccess steps.
Conclusions
When it is all said and done, if you can Scrub, then SCRUB! It provides constant temperature stability. It creates a robust bond (friction breaks oxide and passivation layers). And, the HOTRAIL option maximizes throughput.
We hope you have gleaned some valuable information from this blog series. If you have any questions or comments regarding eutectic die attach, please contact us and one of our die bonding experts are ready to speak with you.