This is Part 2 of "Eutectic Die Bonding 101". There are 10 process variables that exist, four of which Palomar is in the business of controlling (Temperature, Time, Force/Scrub, Gas Environment). The result is a successful void free eutectic die attach.
Before moving forward, I ought to make clear what "void free" means. Only true void free attach can occur in a vacuum. With that being said, when working in reality--that is, in-situ bonding--the industry accepts less than 5% total voiding and 1-2% single voiding.
Below is a great diagram showing the factors influencing voiding under die when eutectic bonding.
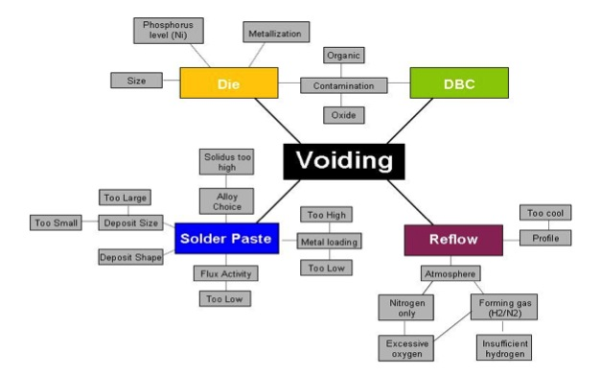
Temperature Effects
As discussed in Part 1, Eutectic means "easily melted". Temperature is at the core of controlling and thereby implementing the eutectic process. Because the eutectic process is a delicate one and voiding is a frequent problem, very tight controls over temperature are imperative. To illustrate the importance of temperature control, here are a few examples: 1) excessive bonding temperature will blister a laser facet coating (rendering the laser useless), 2) solder reaction rates are affected by temperature because the rates increase exponentially with temperature, 3) oxide and passivation layers form rapidly under high temperature (again, creating defects), and 4) "leaching" occurs; creating very susceptible thin film deposits.
Controlling Temperature - Pulse Heat Profiling
Now that we know temperature can negate your entire process, how then is temperature controlled? It must be controlled to get a void free eutectic attach! The way temperature is controlled is with "Pulse Heat Profiling" via a "Pulse Heat Stage" (affixed to the bonder).
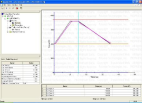
The figure shown on the left is a screen shot of a Pulse Heat Profile. The temperature is ramped up quickly, then a short plateau, then a cool-down period where the attach is solidified.
The benefits of Pulse Heat Profiling are many. First off, it provides closed-loop feedback thereby minimizing overshoot. This prevents laser facet blistering and gives the user higher yield through process repeatability. Secondly, it reduces cycle time (and enhances UPH) with its rapid heating rates. Thirdly, the user is enabled full control of profile through GUI. The benefit is seen in ensuring sufficient bonding time for solder to spread and wick - in short, you get a better joint. Fourth, scrub is not required. This is most important for users of III-V semiconductors, for they are then not in danger of being damaged.
Pulse Heat Payback
The Pulse Heat system is very cost-effective and provides tremendous value in both the short and long term. Making a few assumptions, we can see how Pulse Heat improves yield and pays back:
- $5 per part (cheapest known laser)
- 120 UPH (slow)
- 2 shifts/day
- 1% increase in Yield
In plain terms, it means that using Pulse Heat, the user/customer gets the following financial benefit:
$100 saved per day which accounts to = > $24,000 year
Next up, we will be discussing force/scrub attach and why scrub works for Gold-Tin (AuSn) Solder.
For more information on Automated Eutectic Die Attach, please download the article here.