Yole Développement recently met with David Rasmussen, Assembly Services general manager, to discuss automated die bonding tools for today's evolving LED industry. |

Palomar Technologies has been working with advanced LED designs for over seven years, and was one of the first companies to process matrix LEDs – in modules containing anywhere from six to over 1,000 die. With years of experience, Rasmussen underlined key considerations in using automated bonding in such arrays.
One consideration is that everything is reflowed freestanding, so the die floats which keeps the LEDs from bumping into each other. The amount of flux that you use relative to the size of the LED component you’re placing is important. Then you put down as many LEDs as required for the application, and go through the ramp and reflow process. This process is best achieved using a high-accuracy Pulsed Heat System (PHS) and platform, so parts are not moved after the die are in place.
Learn More about the PHS
|
Matrix LED assemblies are the basis of many systems found in production. Their emerging popularity is derived from their ability to get more lumens per watt from this configuration. However, matrix LED packages present challenges for both die attach and wire bonding compared to single-die packages. High-brightness LED applications require maximum thermal transfer to achieve performance requirements.
The entire reflow process is completed on the same platform, ensuring that the components do not move.
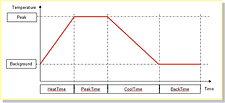
However, LEDs are sensitive to temperatures in excess of 300°C, yet gold/tin reflows in excess of 300°C. The PHS tightly controls the ramp up and cool down very rapidly, which is needed to limit high-temperature exposure.
Once LEDs are attached, wire interconnect is typically completed using strings of wire bonds. A high-density, high-frequency LED matrix format requires LEDs to be interconnected using wires. Although there are several methods of wire bonding, such as ball and wedge bonding, test data indicate that chain bonding interconnects using a ball bonder achieves the best results. In standard ball/stitch bonding, a ball is placed and bonds are placed on top of the stitches to create a string of interconnected LEDs. Chain bonding is a variant on ball/stitch bonding where the stitch is not terminated and another loop-stitch combination is repeated to complete a chain bond wire set.
In addition to LED wire bond processes, Assembly Services also supports precision direct-chip attach (DCA) LED bonding for several years. The DCA process helps minimize design space by eliminating the need for wire bonds. With both anode and cathode terminations on the bottom side of the LED, controlling the amount of flux becomes even more important. You cannot have any bridging between the anode and cathode. Assembly Services has perfected the precision and repeatability of the DCA process, allowing us to support designs with high numbers of LEDs per part.
Lastly, over the past several years, Assembly Services has received inquiries for flip-chip die placement. Flip-chip LEDs are used extensively through the industry. Palomar Technologies die bonders – and therefore, our die bonder customers – have look-up camera capabilities with pattern recognition for precision die placement.
Download the interview transcript to learn more. |
![]() |
----
Jessica Sylvester
Marketing Communications
Palomar Technologies, Inc.