Introduction to the Series
With so much important technological history tied to Hughes Aircraft, it’s hard to believe that more has not been written about this great American technology pioneer. Last October, I authored a blog overviewing Hughes Aircraft’s contributions to avionics, telecommunications and military technologies. Most of that information was uncovered from readily available Palomar Technologies history, plus information available in the public domain. That particular blog generated a tremendous amount of reader feedback. This proved a clear opportunity to dig deeper into Hughes Aircraft’s Industrial Product Division’s roots–to see where this company came from, how it developed over the decades and to lay tribute to the lasting legacy left to us by these brilliant Hughes scientists and engineers. This series is dedicated to those men and women. I would like to thank our readers for encouraging us to dig deeper and tell more of the story. I would also like to thank my co-author, the legendary Hughes Aircraft mechanical engineer William H. Hill who served this company for 50 years, authored numerous patents and provided the core content and verbal history we will share in this series. Enjoy!
Beginnings
This particular telling of the history will begin in the year 1958, in the small Southern California beach town of Oceanside, California. A company called Vacuum Tube Products, Inc. (VTP) was successfully building storage for CRTs, which were used in radar ground systems for the U.S. military. The cathode ray tube (CRT) is a vacuum tube containing one or more electron guns (a source of electrons or electron emitter) and a fluorescent screen used to view images. It has a means to accelerate and deflect the electron beam(s) onto the screen to create the images. To build the storage, spot welders were used (spot welding is a resistance welding method used to join overlapping metal parts). Spot welders were the basis for modern bonding technologies we know today.
At the time, there were only three spot welder manufacturers: Vacuum Tube Products, Unitek and Raytheon. VTP developed their welding technologies via CRT storage technology; Unitek came from the world of orthodontics! Both of these companies were based in Southern California due to the proximity of the large Navy and Marine Corps installations in the region. Hughes Aircraft was one of the largest, if not the largest, VTP customer. In order to get a captive supplier, Hughes Aircraft acquired VTP in 1958. In a larger context, this acquisition represented 1% of Hughes Aircraft’s total business. The name was changed to Hughes Aircraft Industrial Products Division.
The company's location remained as did most of its 100 employees. In 1960, a young engineering graduate from Ohio State University was hired to develop these welding technologies–his name was William H. Hill. A few years later with the company growing, the business moved to the beach town next door (Carlsbad, CA) where it remains today.
Early Technological Developments and Differentiation
The key difference Hughes/VTP offered was the technology of the tube itself. At the time, the CRTs were evacuated glass tubes firing electron guns at the front screen to create a TV flash or image–VTP’s differentiated technology allowed the storage of the image for the first time. This was especially important for military and aerospace applications that required context for images.
Early Interconnection Methods and Equipment
In the early 1960s, the military customers especially were generating high demand for “cordwood” modules. In cordwood construction, axial-leaded components were mounted between two parallel planes. The components were either soldered together with jumper wire, or they were connected to other components by thin nickel ribbon welded at right angles onto the component leads (note: these packages were quickly phased out by the advent of reliable production worthy semiconductor and PCB technology in the 1970s).
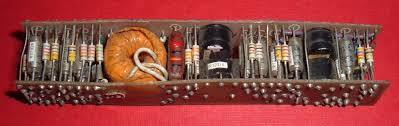
The Hughes Industrial Products Assembly and Test Division portion were making breakthroughs working on the following welding and soldering technologies to meet the expanding customer requirements:
-
Spot Welders: using small wire, small sheet metal. The end user applications were military, space, and appliances. The “welded electronic packages” were made of axial lead components interconnected by 10x31 mil nickel ribbon. Note that these were all assembled by manual machines at the time–all manual operators with foot pedals and a microscope.
-
Parallel Gap Welding with Multi-Lead Components: using welders to connect multi-lead component or flat packs. The purpose of parallel gap welding was to introduce current on one side and let it come out the other. Using a very short heating pulse allowed the engineers to weld these components onto a circuit board.
-
Pulse Heat Soldering: using a loop made of resistance heater materials. Flat packs were solder-coated and required interconnection. Pulse heat soldering technology was the answer (customers were using solder, not gold).
Part 2 of this series will cover developments of pulsed heat technologies to bonding wire; using pulse heating of a capillary to bond gold wire.
Learn more about pulsed heat technology used today:
Article references:
REF: http://en.wikipedia.org/wiki/Cathode_ray_tube#History
REF: http://planefinder.net/about/the-history-of-flight-radar/
REF: http://en.wikipedia.org/wiki/Printed_circuit_board#Cordwood_construction
Richard Hueners
Director of Sales and Marketing
Palomar Technologies, Inc.
William H. Hill
Former Hughes Aircraft/Palomar Technologies Mechanical Engineer