Wire bonding is the most robust and commonly used method for chip-to-die interconnection of lead-frame, integrated circuit (IC) packages, RF microwave packages, and optoelectronic packages.
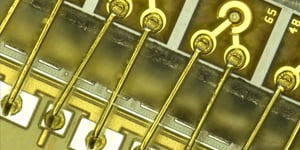
Gold Wire Bonding
Gold wire bonding is the process by which gold wire is attached to two points in an assembly to form an interconnection or an electrically conductive path. Heat, ultrasonics, and force are all employed to form the attachment points for the gold wire.
Aluminum Wire Bonding
Aluminum wire bonding is a process similar to gold wire bonding but with the key distinction that the surface does not need to be heated to 150C or even anything above room temperature.
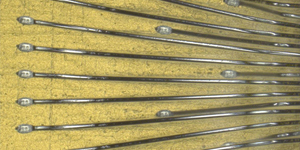
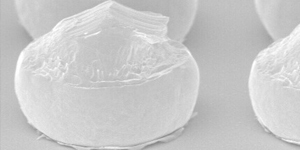
Ball Bumping
Ball bumping is an important process in flip-chip applications as it provides the necessary interconnects between chip and substrate. Ball bumping can be performed at the assembly or wafer level.
Wedge Bonding
Wedge bonding utilizes a wedge tool to form the stitches on both ends, without the use of a ball for the first bond. The bonds themselves a thin and wedge-shaped.
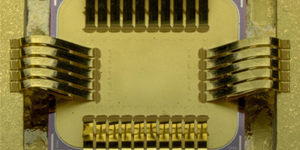